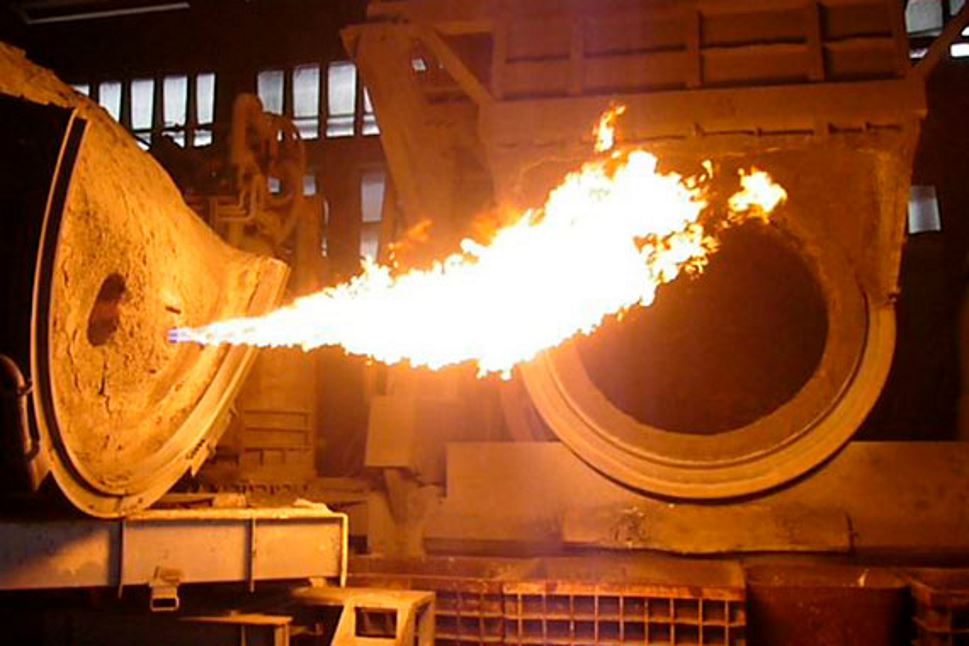
Innovative Solutions and Operational Excellence
Air Products continually innovates burner technologies with a variety of flame shapes, heat release profiles, and mounting configurations to meet the varying needs of secondary melters. In addition, we use optimization algorithms, to standardize production cycles and improve repeatability.
Air Products' offerings that feature Process Intelligence use sensor and communications technology to monitor and control our gases and equipment, as well as track key process parameters. Your personnel can remotely access this data for improved process understanding.
ADVANCED CLEAN ENERGY LABORATORY—VIRTUAL DEMONSTRATIONS TO GLOBAL LOCATIONS
The Advanced Clean Energy Laboratory is our newest demonstration facility, capable of facilitating development and full-scale testing of combustion systems using actual customer fuels. Plus a remote video imaging system enables real-time participation in testing via the Internet.
Transient Heating Oxy-fuel Burner
With Air Products’ patented Transient Heating burner, you can achieve more even heating throughout your reverb furnace, eliminate cold zones, and maximize melt rates.
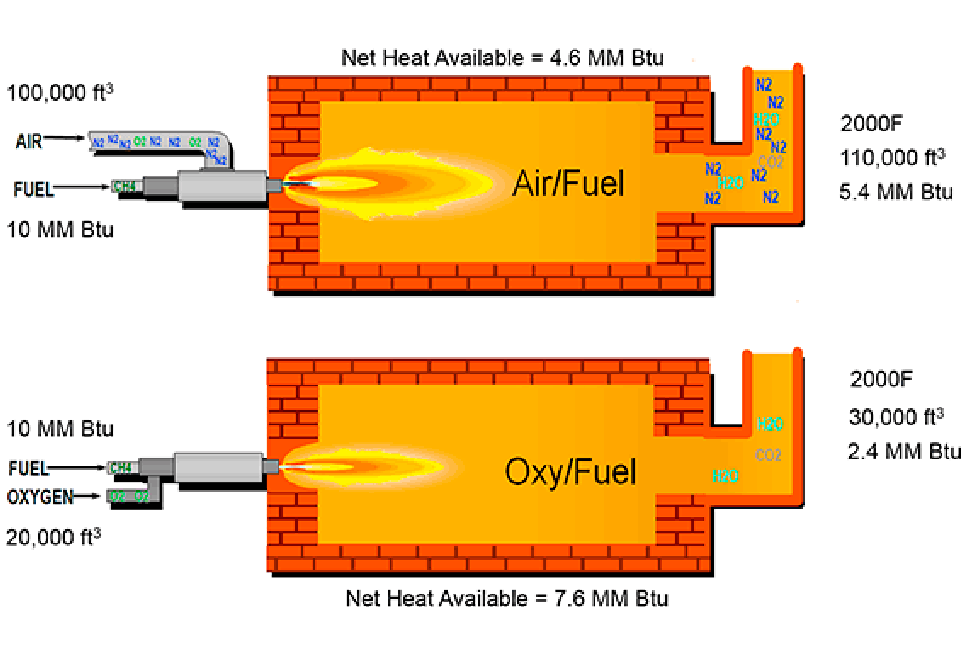
Available Heat Comparison: Air-fuel vs. Oxy-fuel Combustion
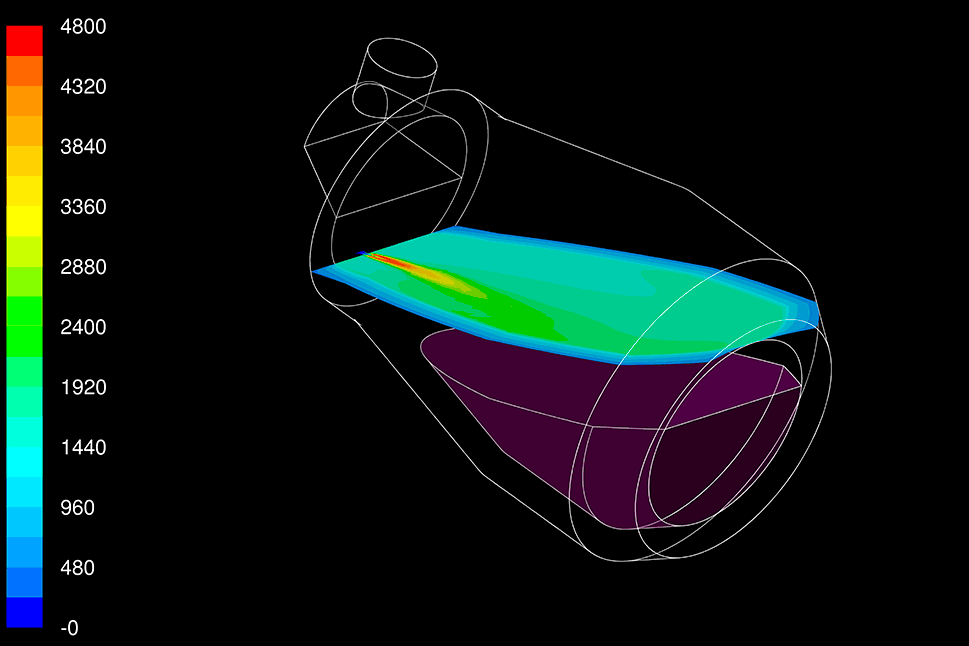
Proven Computational Fluid Dynamics Modeling Services for Secondary Non-ferrous Melting
Computational fluid dynamic (CFD) modeling can be a powerful tool to assess and optimize your process. We have extensive in-house CFD modeling capabilities that can help evaluate and investigate ways to increase productivity and reduce costs with burner selection and furnace updates customized to your specific operational goals.
Learn More
Count on Air Products' expertise…
We can help you determine the optimal solution to your operational challenges and suggest ways to boost your production.
Resource Center
Technical Articles
- Oxy-Fuel Technologies and Strategies for Secondary Aluminum Melting Operations, Light Metal Age
- Customized Combustion Solution Yields Productivity Improvement for Aluminum Extruder
- New Burner Technology: Turning Low-grade Scrap Metal into High-efficiency Savings
- Effective Use of Oxy-fuel Combustion in Aluminum Reverberatory Furnaces, Light Metal Age
- Combustion Technologies Improve Melting Furnace Productivity, Industrial Heating
- Oxy-Fuel Technologies and Strategies for Secondary Aluminum Melting Operations, Light Metal Age